By Ryan Bergman
Pulse width modulated (PWM) sprayer nozzle technology has been present in the ag industry for many years. These systems can maintain pressure as speed changes by adjusting the duty cycle of the nozzle, allowing more or less product to flow out. Many systems also offer individual nozzle section control, which can reduce overapplication of product at headlands and around field obstacles. Another key benefit of these systems that is not often well understood is turn compensation.
As your sprayer turns around an obstacle in a field—driving around the edge of a waterway, for example—the inside boom (closest to the waterway) will travel significantly slower than the outside edge of the boom. Standard spray systems do not account for these changes in speed across the boom and product will still be applied based on the speed the chassis is traveling at. On a sprayer with a large boom, this can lead to problematic over- and under-applications.
To illustrate this problem and the benefits of PWM nozzle technology, a self-propelled sprayer equipped with a 120-foot boom was driven in a circle applying blue dye in a water carrier using a traditional spray setup on half of the circle and using PWM technology on the other half. The inner circle is 40 feet in diameter and would simulate driving around the tip of a 40-foot wide waterway.
As shown in Figure 1, the top half of the circle was applied with the sprayer operating in a traditional spray mode with no PWM technology activated. An overapplication by the inside boom wing can be clearly seen, as it was traveling at about 25 percent of the targeted ground speed (2.5 miles per hour) and applying nearly 40 gallons per acre. In the middle of the sprayer path, the speed and rate were on target at 10 miles per hour and 10 gallons per acre. On the outside of the spray boom in the top half of the circle, the application rate is slightly under the target rate at about 6 gallons per acre. This can be seen by the slightly lighter coverage on the edge of the circle. This is caused by the outside of the boom traveling at about 17.5 miles per hour.
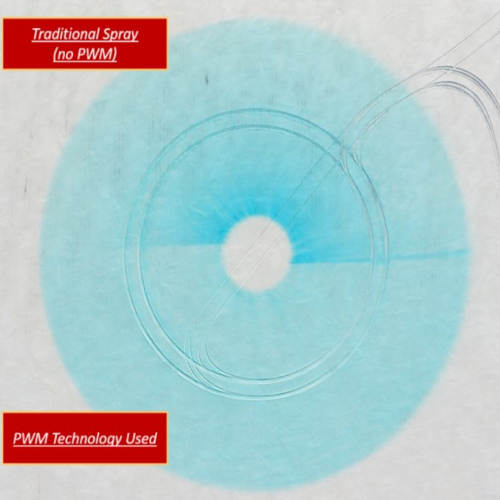
Figure 1. Demonstration of spray coverage and application rate when using a traditional sprayer setup (top half of circle) compared with utilizing a PWM spray system with turn compensation (bottom half of circle).