Platform wrappers cover individual bales. Most platform wrappers pickup, wrap and dump bales as an operation following baling. However, some newer balers incorporate a wrapper that completes both operations in one pass. Most platform wrappers cost less to purchase than in-line wrappers. Other advantages of platform wrappers include: a hole in the plastic of one bale only spoils that bale, bales can be fed at any rate needed, and bales can be marketed more easily. The main disadvantages of a platform wrapper are plastic cost and the time required to wrap each bale. Also, users need a special loader attachment (clamp) to pick up and move bales without damaging the plastic.
In-line wrappers place the bales end-to-end and wrap the outside of the bales. Operators manually cover the ends of the first and last bale or insert a few "junk bales" at the beginning and end of each row to seal it. The end product looks like a long tube of bales.
An in-line wrapper uses less than half as much plastic as a platform wrapper and requires less labor per bale. However, bales are less marketable to distant customers, and once a producer opens a row, the bales need to be fed at a constant rate to avoid spoilage. Air temperature governs the spoilage rate; spoilage is slowest in cool weather, allowing for a slower feeding rate if needed.
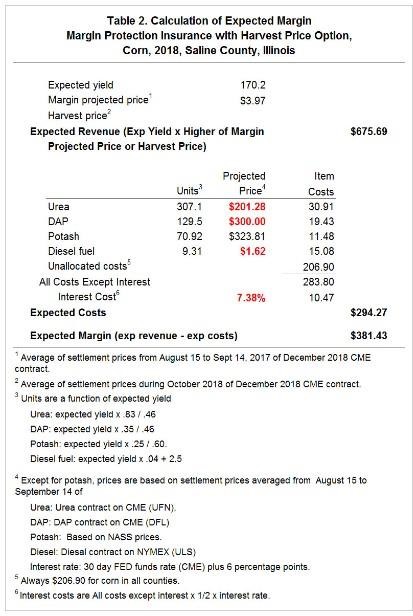
If you decide to make some baleage this year, a few tips follow:
- The ideal moisture for baleage is 45 to 60%. This moisture content allows for complete fermentation of the forage. However, moisture contents down to 30% (sometimes called 'tough hay') still works.
- Make dense, consistently sized, tight bales. Usually, round bales should be only 48 to 54" tall. Remember, the bales will be heavier than dry hay because of the additional water content. Tie bales with net wrap, natural fiber twine, or plastic twine. Avoid treated sisal twine.
- Wrap bales with a good-quality, 1-mil plastic resistant to sunlight with a minimum of four layers of plastic with a 50% overlap. Six layers are better.
- Wrap bales within 24 hours of baling. Sooner is better.
- Store baleage on a well-drained site, close to the intended feeding area. Patch holes promptly – use UV-protected plastic tape if available. If not, duct tape works in a pinch.
- Consider how you will dispose of the plastic at feeding time. Recycling is best when available.
Source : missouri.edu