By R.L. (Bob) Nielsen
Understand this one simple fact about grain yield monitors: They do not measure grain yield.
How's that for an opening statement?
Flow sensorWhat I want you to understand is that yield monitors ESTIMATE yield by converting electrical signals received from a mass impact or optical sensor, located somewhere in the clean grain elevator of the combine, into ESTIMATES of grain flow (lbs) per second or two of travel time. Along with ESTIMATES of distance traveled (usually based on differentially corrected GPS signals), header width, and ESTIMATES of grain moisture content... the yield monitor's firmware / software then ESTIMATES "dry" grain yield per acre, at a moisture content of your choice, and records those yield estimates, and their geographic location in the field, every second or two in the display's memory or uploaded by cellular connection to a Cloud-based Web server.
Yield monitor calibration involves a series of steps to ensure that the ESTIMATION of each of these factors is accurate. One of those steps involves the harvesting of calibration "loads" of grain that are used to "teach" the yield monitor's "black box" how to accurately convert the electrical signals from the sensors into ESTIMATES of grain flow rates.
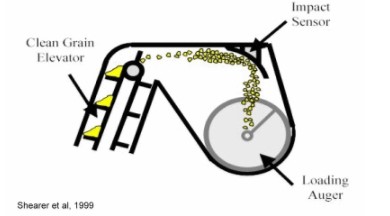
The calibration "loads" should be harvested in such a way as to mimic the range of grain flow rates (i.e., the range of yield) you expect to encounter when harvesting a field. Ideally, each calibration load is calibrated at a different, but uniform grain flow rate. Some folks harvest strips at different speeds to accomplish this. Some folks harvest strips of varying widths (full header, 3/4 header, 1/2 header, etc.). In our field-scale nitrogen research trials where we have a wide range of N rate strips, our calibration loads typically come from 5 to 6 different N treatment rates because that often provides the greatest range of potential grain flow rates.
Yield estimates on a whole field or individual load basis made by a well-calibrated yield monitor are accurate in the sense that they often very closely match yield estimates calculated from weigh wagons or commercial weigh scales. However, to achieve a satisfactory level of accuracy, yield monitors must be "trained" to correctly interpret the electrical signals created by the impact sensor into estimates of grain flow rate . Some background information may help you better understand the nature of and importance of faithfully and regularly calibrating yield monitors.
Calibrating a yield monitor simply requires the harvest of individual "loads" of grain that represent the range of grain flow rates (i.e., a range of yield levels) expected in the field(s) to be harvested.The amount of grain required for each calibration "load" ranges from 3,000 to 6,000 lbs (50 to 100 bu grain) depending on the manufacturer's recommendations for the specific model/make of yield monitor. The grain weight of each "load" is estimated "on the go" by the yield monitor as the grain is harvested. The grain for that specific "load" is then offloaded from the combine hopper and weighed on calibrated or "known to be accurate" weigh wagon or commercial scales. The actual weight is then entered into the yield monitor console and the yield monitor firmware makes mathematical adjustments to the calibration response curve.
Conceptually, the calibration process involves fitting a response curve between grain flow rate and flow sensor signal strength in order to estimate low, medium, and high yields. Makes of monitors appear to differ in the nature of the calibration curve that is determined.
Some manufacturers suggest that only one grain load is necessary to perform an accurate calibration. That recommendation implies the calibration response curve is a straight-line or near-linear relationship between grain flow rates and flow sensor signals. While the standard recommendation is for only one grain load, the "fine print" in the owners' manual suggests that additional calibration loads may be added to fine-tune the accuracy when necessary.
Other manufacturers recommend between 3 and 6 grain loads are required to perform a satisfactory calibration of the yield monitor. This recommendation suggests that the calibration response curve for these yield monitors is not a straight-line, but is rather some sort of non-linear response curve that requires a number of calibration points to best "train" the yield monitor how to interpret the flow sensor signals.
The goal with multi-load calibration procedures is to "capture" the full range of grain flow rates (aka yield levels) you expect to encounter during the harvest of your fields. Capturing a range of grain flow rates during calibration can be a nuisance because it typically requires harvesting individual full header-width "loads" at different speeds or partial header-width "loads" at a constant speed. This headache plus the time it takes to off-load and weigh the individual grain loads are among the most common reasons why growers do not faithfully or routinely calibrate their yield monitors.
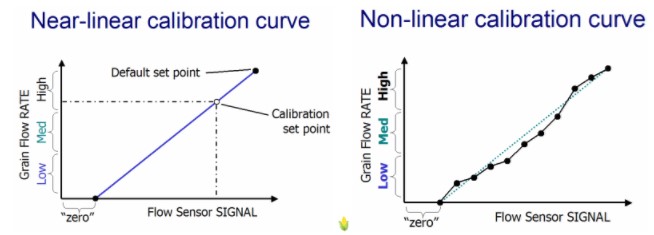
Yield monitor accuracy can be excellent if the yield monitor is well-calibrated. Yield estimates by calibrated yield monitors that I use in my field-scale research trials are typically within 1 % or less of the actual grain weight measured with a weigh wagon or farm scales. Conversely, yield estimates can be very poor if yield monitors are not well-calibrated. The error in accuracy can be as much as 100 % if the yield monitor is taken "off the shelf" and put into service without any calibration. Errors in accuracy can easily range as high as 7 to 10 % late in harvest season if the yield monitor was calibrated only at the beginning of the harvest season because of changes in grain moisture content. Errors in yield estimates are especially likely if the full anticipated range of harvested grain flow rates are not included in the calibration of the yield monitor.
Well, you may ask... who cares whether or not your yield monitor is providing you with accurate yield estimates? After all, growers are typically paid at the point of sale according to the net grain weights printed on the scale ticket and not according to a yield map. Quite honestly, accurate yield monitor estimates also may not matter for simple farm record-keeping purposes.
However, if you want to USE the information that an accurate yield dataset provides, then you should strive to ensure accuracy in the yield estimates made by your yield monitor. Common uses for yield monitor data include comparisons of one field to another, one specific spot in a field to another, one hybrid's performance to another, early versus late harvest season, and experimental treatments in on-farm field trials.
Yield monitor calibration accuracy can be influenced by yield levels outside the range of grain flow rates used for the yield monitor calibration, by seasonal changes in temperature, by seasonal changes in grain moisture content, by hybrids in terms of their differences for grain weight, grain shape, and grain moisture, and by field topography. Calibrating your yield monitor once a season will not assure that it remains accurate the entire season. Check the accuracy of the yield monitor calibration occasionally by harvesting and weighing additional calibration loads. Recalibrate the yield monitor when necessary to maintain an acceptable accuracy.
Don't forget to...
- Also calibrate the combine's grain moisture sensor.
- Also calibrate for the zero-flow combine vibration.
- Also calibrate the temperature sensor at the beginning of the season.
- Re-read the yield monitor operations manual prior to the harvest season.
- Create a pre-season and in-season yield monitor checklist of all adjustments and settings.
- Go through the yield monitor checklist every morning before beginning the day's harvest.
Bottom Line
Yield data can be very useful for identifying and diagnosing yield influencing factors in corn or soybean. Yield monitors can also be useful for harvesting on-farm research trials. Yield monitor calibration, yield data processing, and yield data "cleaning" are necessary to ensure accurate yield data.
The bottom line is that extra care and attention to details are important when calibrating yield monitors. Dig out that users guide for your yield monitor system NOW. Before the end of summer, devote some quality time to reading the sections on yield monitor calibration. Familiarize yourself with all aspects of yield monitor calibration. Attend a yield monitor workshop. Create your own checklist of calibration steps and follow them faithfully every time you calibrate the monitor. Do not forget the little things like vibration settings, header height stops, offset of the DGPS antenna, etc. Recognize that accurate weighing devices (grain carts, weigh wagons, farm scales) and moisture meters are crucial for the calibration of the monitor's wet weight estimates and adjusting the combine's moisture sensor readings.
And remember the old adage about computers: "Garbage in equals garbage out".