By John
Thanks to the weather we had this year, corn is variable across fields and in some areas we will be harvesting corn at higher moistures than normal. Stalk quality may also be variable by field and amount of stress the plant was under, see the article Stalk Quality Concerns in this weeks CORN Newsletter. This variability and high moisture may require us to look harder at combine settings to keep the valuable grain going into the bin. Each ¾ pound ear per 1/100 of an acre equals 1 bushel of loss per acre. This is one ear per 6, 30 inch rows in 29 feet of length. A pre harvest loss assessment will help with determining if your combine is set properly. Initial settings for different combines can be found in the operator’s manual but here are a few adjustments that can be used to help set all machines. Thanks to the weather we had this year, corn is variable across fields and in some areas we will be harvesting corn at higher moistures than normal. Stalk quality may also be variable by field and amount of stress the plant was under, see the article Stalk Quality Concerns in this weeks CORN Newsletter. This variability and high moisture may require us to look harder at combine settings to keep the valuable grain going into the bin. Each ¾ pound ear per 1/100 of an acre equals 1 bushel of loss per acre. This is one ear per 6, 30 inch rows in 29 feet of length. A pre harvest loss assessment will help with determining if your combine is set properly. Initial settings for different combines can be found in the operator’s manual but here are a few adjustments that can be used to help set all machines.
Corn Head
Setting the combine starts at the header with an average of 66% of all machine harvest loss in corn occurring here. The major adjustments on the header are deck plate width and gathering chain speed. Setting deck plates in variable field conditions can be challenging, hydraulic adjust deck plates help a lot but if they are not automatic adjust you will have to keep up with changing conditions throughout the field. Under normal conditions deck plates should be set to 1 ¼ inches in the front and 1/8 inch wider at the back, 1 3/8 inches. While this is a starting point, a better method is to use actual stalks of corn and set the deck plates 1/16 of an inch wider at the front than the third node width of a corn stalk. If you check the best and the worst corn in the field you should be able to get an idea of how to vary deck plates on the go, possibly make marks on the indicator gauge to know where you want to be in each area. The basic goal is to keep deck plates narrow enough that we avoid butt shelling and ears slipping between the plates into the stock roll but still manage to be wide enough that most of the stalk and leaves get pulled though. If stalk lodging is present, increase deck plate taper, more open at the top will decrease fodder entering the combine. The other major setting is matching gathering chain and stalk roll speed to combine ground speed, which can be a challenge if you cannot vary header speed from the combine cab. The threshing system works best when full so we speed up in lower yielding areas but if the gathering chains/stalk rolls don’t change speed our header loss will increase. This leads to another balancing act of increasing speed for harvest efficiency and seeing increased grain loss. If ground speed is 4 mph gathering chains should be running at 55 rpm. With the ratio staying constant across all ground speeds. Chain lugs should be opposite each other. With variable field conditions, making sure your rubber ear savers are present and flexible will retain whole ears from being lost.
Threshing
If the header worked properly there will not be a great deal of fodder in the threshing system, increased fodder leads to higher threshing losses. The first consideration in threshing settings is cob integrity, which is often compromised in stressed and high moisture corn. When setting concaves the goal is to not break cobs into more than 2 pieces crosswise and not break them length wise at all. The initial concave clearance on most machines is 3mm over cob diameter. Cobs should be coming out the back of the machine intact but when you break them in half, there should be signs of compression. Rotor or cylinder speed should be set using your book and only sped up if concave clearance is set and ears are still not threshed. Increasing rotor speed can increase threshing quality without breaking cobs, better than tightening concave settings. In wet corn, damaged grain is more often caused by high rotor speed than narrow concave settings. When harvesting high moisture corn, technically anything over 22%, according to most manufacturers, different concaves can help with threshing. Changing the large wire concaves to round bar, either straight or fish bone helps maintain cob integrity and grain quality in wet corn. Extremely wet corn, over 30% moisture, will need round bar concaves to maintain threshing grain quality. Wet corn can be damaged much more easily during threshing.
Cleaning shoe
The last settings are in the cleaning shoe, fan speed and sieve opening. In corn, especially wet corn, most if not all of the separation and cleaning should take place on the top sieve. For dry corn, the lower sieve should be closed a little tighter than the top sieve. In wet corn, many manufacturers recommend opening the bottom sieve all the way so that corn easily moves into the clean grain elevator and does not over load the tailings auger. All the separation is then taking place on the top sieve. A common starting opening is 5/8 inch, then open until the first cob appears in the grain tank and shut one notch. A challenge this fall will be with kernel size. Even wet kernels may be smaller than average this year causing you to need a top sieve opening to be less than 5/8 inch. Kernel size will have increased variability, ears with many aborted kernels will have much large kernels than those on normal ears. Fan speed should be increased until all red chaff is gone from the grain tank then slowed down 30-50 rpms to keep grain from being blown out the back. This may actually be at lower rpms this year than most years due to low test weight which makes each kernel lighter than normal and more likely to blow out of the machine. Often fan speed settings are opposite of logic, increasing fan speed often decreases losses because chaff floats more allowing grain to fall through the sieves better.
Checking harvest loss and combine settings
When assessing combine settings there are four areas of loss to consider. The first is preharvest lost which is one ¾ pound ear per 1/100 of an acre which is one ear in 30 inch rows per 29 feet in 6 rows or 21.8 feet in 8 rows. The next source of loss is header loss, then threshing and sieve loss. When counting individual kernels, 2 kernels per square foot equally distributed equals one bushel pre acre. In order to determine which part of the combine to adjust you need to calculate loss from each area. To check header loss stop the combine and back up the length of your combine. Then for 30 inch rows count the number of kernels in front of the combine from center of row to center of row for 4 feet of length which equals 10 square feet and divide by 20 to get bushels per acre. Each row of your header should be checked, since only one may be out of adjustment, record each row separately. Also check for additional ears that may have been lost by the header and not pre harvest, remember one ¾ pound ear per 1/100 of an acre equals a bushel. Record header loss to subtract from separator and cylinder loss. Preform the same kernel count behind the machine as you did in front subtract each row individually from header loss calculate separation loss. Watch for any cobs that still have corn on them this is threshing loss count these separate. A study conducted in Iowa found the best set combines have a total loss, pre and post-harvest loss, of 1.5 bushel per acre. Use the table below to calculate losses, remember kernels per 10 sq ft divided buy 20 equal bushels per acre.
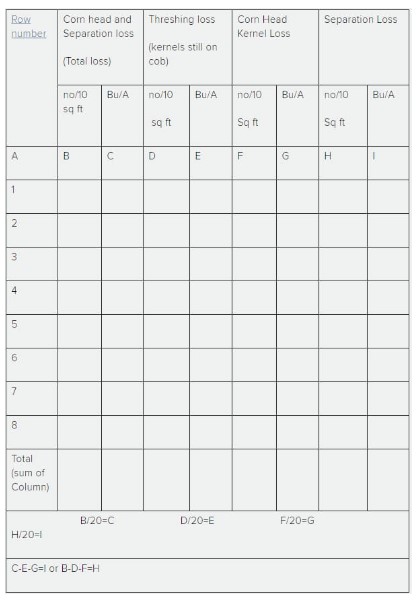
Setting Harvest Loss/Tattletale Monitors
Once your machine is set to expected harvest losses, adjust your loss monitors in order to use these monitors in the field. Harvest lost monitors work by sensing grain impact on the sensors, grain size and sensitivity can be adjusted to calibrate these loss monitors. Larger grain hits more area on the sensor increasing loss values. Larger harder grain also hits with more force. Usually you adjust grain size and then sensitivity. Good luck with harvest this fall.