By Stephen Brown and Linda Fetzer
Using an effective LOTO system can prevent incidents, injuries and potential fatalities associated with flowing grain hazards.The most common example of LOTO in production agriculture is using it when a person enters a grain bin. LOTO should be used whenever a person goes into a grain bin to do any service or maintenance (e.g., unclog an auger). It is vital that the power is turned off to the equipment and a lockout/tag out process is used to prevent someone from engaging power and causing a potentially life-threatening incident.
LOTO Components
LOTO kits can be purchased from your local grain bin company or from a reputable online agricultural supply site. Figure 1 shows a purchased LOTO kit. Typically, the kits include multiple locks with lock specific keys, locking devices, and tags. The LOTO kit or wall mounted station should be in an area accessible to all workers and annual training on this process should be provided to the workers. New workers should be trained on the LOTO procedure before they begin work on the farm. Training should enable workers to understand the importance of energy control and have the skills to follow the LOTO process.
The LOTO Process
The LOTO process as defined by the Occupational Safety and Health Administration (OSHA) standard 1910.147 involves a total of eight steps. The first step is to review and understand the procedures required for safely shutting down the equipment. Next is to notify others about the scheduled shut down. Once employees are notified, the equipment can be shut down by following the proper procedures outlined in Step 1. After the equipment is shut down, it is important to ensure that all primary and secondary energy sources are secured, and the equipment cannot be unintentionally energized. To verify that the lock out procedure is effective, ensure that everyone is clear, and attempt to start the equipment. If the equipment remains deenergized, the next step is to install a locking device to the energy control component that is compatible with that specific application (e.g electric breakers) and a documentation tag that states when (e.g., date, time, etc.) and why (e.g., repair, maintenance, etc.) the system was locked out and the names of those people performing the maintenance. This locking device and documentation tag should be secured by a pad lock by each person performing work, paired with a key specific to their lock that should be kept by them (See Figure 2).
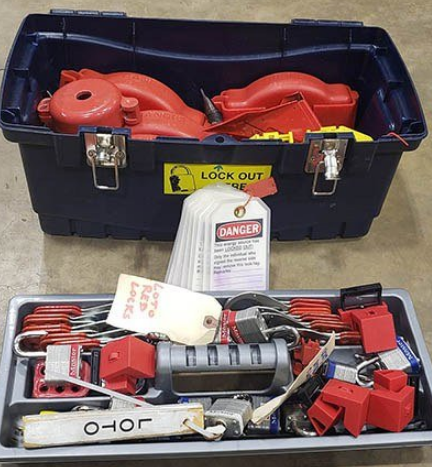
Once the LOTO process is complete, it is safe to begin the service or maintenance work. Once the work is completed, clean up the work areas and make sure that people are a safe distance from the bin. Notify the people around the bin that work will resume. The person who completed the LOTO should be the only person permitted to remove it which ensures that the system is not started by another person. Finally, remove the lock out devices and start the equipment and monitor that is it working properly.
Conclusion
Best practices to promote safety around grain bins are multi-faceted. LOTO is just one of the best practices and needs to be used in conjunction with personal protective equipment (e.g., respirators, earplugs, eye protections, etc.), fall protection system that includes a body harness and a lifeline, and keep equipment in good operating condition. Reducing the risk of an injury or fatality to a family member or employee is the primary goal of implementing safe operating procedures on farm operations.