By Ronald T. Schuler, Extension Agricultural Engineer, Biological Systems Engineering
A properly adjusted crop processor on a forage harvester will break all the corn kernels and have no large cob pieces remaining in the corn silage. The primary processor adjustment to achieve this goal is the clearance between the processing rolls. The clearance should be sufficiently small to break nearly all the kernels but not too small to create excessively high power requirements. Also a very small clearance will cause excessive wear on the processing rolls.
Since the crop processor adds to the power requirement of the forage harvester and may reduce the harvesting capacity, some machine operators attempt to adjust the roll clearance to the largest possible while maintaining crop quality based on kernel breakage. Recent studies indicate there is an adjustment which can meet both goals.
Studies at the University of Wisconsin evaluated the impact of crop processing roll clearance on the corn silage characteristics and energy requirements. Jirovec et al,1999, conducted studies over two seasons (1997 and 1998) and at a crop maturity ranging from one-third to three-quarters milk line. They evaluated particle length, kernel breakage, cob breakage and energy requirements using the averages for three samples taken from each treatment and for the maturities during each season.
In their 1997 study, they obtained 100 percent kernel breakage with a theoretical length of cut (TLC) of 3/4 inch and a roll clearance of 0.04 inches (Table 1). At a clearance of 0.12 in. the kernel breakage was 91 percent. These are significantly lower than the non- processed silage where the kernel breakage was 63 and 50 percent respectively for 3/8 and 3/4 TLC. The mean particle length of the corn silage was reduced by the crop processor but not below the results obtained from the 3/8 in TLC and no processing.
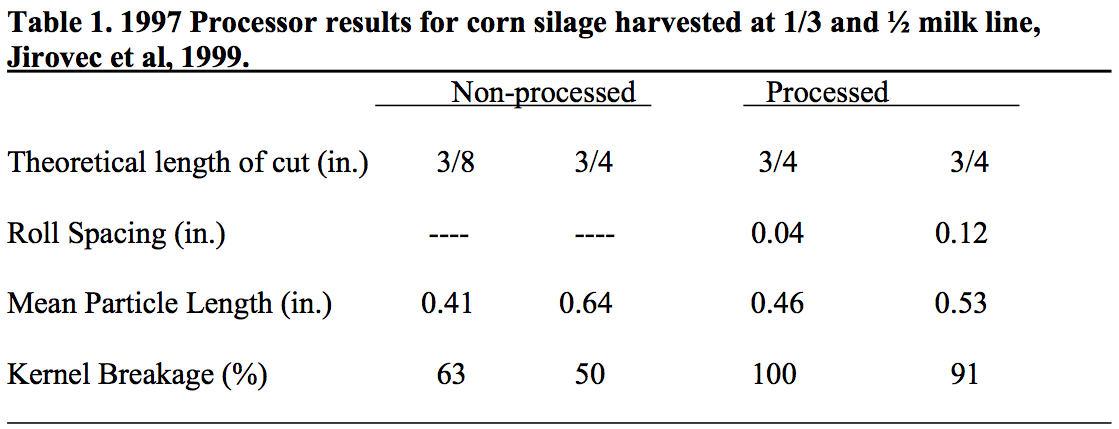
In 1998, they evaluated silage at three maturities (1/3, 1/2, and 3/4) and added a roll clearance of 0.20 in. They also evaluated cob breakage and the power requirements for these treatments. The 1998 results indicate slightly improved kernel breakage, which can be partially attributed to the 3/4 milk line treatment that was added. As the crop matures, the kernel breakage improves. The cob breakage was complete for all three roll clearance settings. For the non-processed setting, some whole cob pieces remained.
The energy requirements were calculated from data collected from torque and speed sensors on the forage harvester and is in terms of horsepower-hours per ton (energy per ton). The fuel requirements were estimated by using American Society of Agricultural Engineers recommendations and were for operating the chopper. It does not include the tractive power.
The feed rate through the forage harvester, Table 3, ranged from 35.6 to 39.0 tons per hour. There were no significant differences among the operating conditions. The crop processor increased the energy requirement for the chopper, Table 3. The energy requirement at the 0.04 in clearance (2.99) was significantly higher than the 0.08 (2.76) and 0.12 (2.70) in clearances. The difference between 0.8 and 0.12 was not significant.
The fuel consumption trends are the same as the energy requirements for the chopper. The 0.04 in. roll clearance had the highest fuel requirement, 0.019 gallons per ton more than the 0.12 in clearance, Table 3. The difference is estimated at 0.7 gallon per hour. Again the difference between 0.12 and 0.20 clearance was not significant.
In summary the recommended roll clearance should be between 0.04 and 0.12 in. with TLC of 3/4 inch. At this setting, all the cob pieces will be broken and the broken kernels will exceed 90 percent. Adjusting the clearance closer to the 0.12 in. will not create an excessive power and fuel requirement.