Part of increasing quality is decreasing contaminants. This can be done through management throughout the year or skirting during shearing. The major three wool contaminants are: polypropylene twine, vegetable matter, and hair/medullated fibers or black fibers.
Polypropylene twine is difficult to card out and has the potential to show up in the final product. Twine is commonly used to secure gates and panels but limiting its use and making sure that it is picked up can reduce its potential of contaminating a clip. Additionally, wool should be packaged in new packs or burlap sacks. Putting small wool clips in polypropylene feed sacks can increase contamination, especially if the bag starts to shred.
High levels of vegetable matter can decrease yield and take extra time to remove during the manufacturing process. Although technology during the scouring stage (acid wash) removes excess vegetable matter, it may not be implemented by all mills. Management changes, like feeding closer to the ground, chopping forages or using straw bedding can help reduce vegetable matter. Removing high hay-chaff areas, such as the poll, crow’s nest (where neck and shoulder meet) and belly, from the main wool clip during shearing can also increase value.
Medullated fibers and hair are hollow fibers coarser than wool fibers. They do not accept dye and can compromise final products. Sorting out caps and bellies during shearing may reduce these unwanted fibers. Being mindful of shearing order is also important. Always shear wool breeds first, followed by black face or coarser breeds. If an operation includes hair sheep, they should always be kept separate, if possible, from the wool breeds.
Skirting and Classing
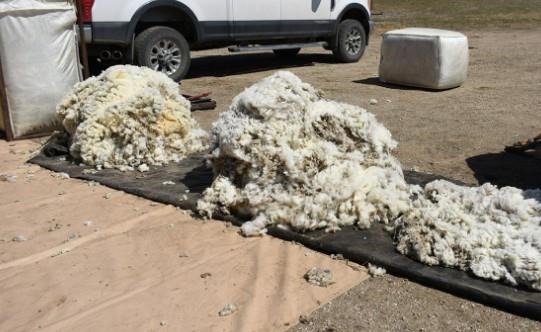
Figure 2. Fleeces skirted bellies out untied and sorted off for short or tender and heavy staining. Belly wool is placed in separate bag (upper left).
Skirting is the process of removing inferior portions of a fleece. Typically, this is done by the producer or wool classer during shearing. A light skirting may be Bellies Out Untied (BOU). Bellies and caps are the first parts of the sheep shorn, so removal is quick and easy. In comparison, a full-table skirt includes throwing the fleece onto a slatted table to remove bellies, locks/tags, second cuts and any other inferior wool. Fleeces should always be rolled cut-side out. Although both preparation methods improve wool quality, higher prices are usually given when fleeces are prepared with a full-table skirt.
Classing wool creates more uniform bales by grouping similar fleeces based primarily on length, strength and fiber diameter. Wool classers visually group fleeces into finer-than-average, average, and coarser-than-average, or the AA, A and A-1 lines. The degree to which fleeces are sorted and the number of lines is based on producer preferences. Lines are often determined based on current wool prices and the number of fleeces that fall outside the average. Ram, lamb and short stapled/tender fleeces are also commonly sorted from the main, or A line. Although classing improves consistency within bales, forming full bales is more cost-efficient than greater fragmentation of classing lines and creation of smaller lots. Trained personnel are required for classing, and some shearing crews have certified classers. However, Level-1 classing certification can be obtained by producers to class their own fleeces by attending wool classing school.
Pricing Wool
Some buyers heavily discount for excessive amounts of any type of contamination, as described above. Skirting and classing fleeces on the shearing floor and management decisions prior to shearing to minimize contamination is likely to return additional profits for the producer.
Furthermore, significant price-per-pound differences are often seen between low-20 micron (≤23 µm) and mid-to-upper-20 micron (≥24 µm) wools. For example, a 22-micron fleece with a clean price of $3.50 per pound and a 57% yield will have a greasy price of $2 per pound. Whereas a 24-micron fleece valued at $3 per pound with the same yield would be worth $1.71 per pound. That is a 29 cents-per-pound difference by increasing just two microns. Pricing is also heavily determined by yield. Wool buyers may lower prices for lower yields due to the additional processing required by the mill to scour low-yielding wool.
Calculating Wool Price
Wool prices are reported as clean wool price but rewarded on a greasy basis. Here is how to calculate the price of raw wool:
Micron: 22 µm
Yield: 57%
Staple Length: 82.55 mm (3.25 in)
- Clean wool price: $3.50/lb.
- Greasy Price (Clean price × yield):
- $3.50 × 0.57 = $2/lb.
- *10–15 cents may be charged for a handling fee:
- $2 - $0.10 = $1.90/lb.
*Additional discounts may be given based on strength, length and yield. Discounts vary among buyers.
Final Thoughts
Although finer wool receives higher prices, production goals should be specific to breed type. Not all breeds of wool sheep are genetically fine wooled (<23 µm). Coarser wools are more desirable for hand-spinning, yarn, and outer layers due to their increased strength and durability. Additionally, breeding for fineness can decrease yield and weight, so individual goals must be evaluated to achieve target micron and clean wool yield/weight for the breed in production. However, regardless of breed or micron, mitigating contaminants and inferior wool fibers in a clip will increase its overall value.
Source : sdstate.edu