To fully understand the importance of the EMC, knowledge of how wood reacts to moisture loss and gain is needed. As wood dries below 30% MC it begins to shrink in both thickness and width. Each species shrinks slightly different amounts but in general most of our hardwoods in Pennsylvania will shrink between 6% and 8% if it is completely dried. One of the reasons we dry lumber is to get the shrinkage done before the lumber is used to build a product. Otherwise, there will be issues with broken glue joints, warp, and drawers that stick, to name a few. Since wood will also gain moisture if the conditions are right, wood will expand as a result of gaining moisture causing the same issues as shrinkage.
Is air drying good enough for the lumber in your project? That depends on where the product will end up. Will it end up in an unheated shed or in the house? What is the average EMC where the product is going to be used? If lumber is air dried to 13% MC and then made into a product such as an end table and brought inside where the EMC is 5%, the wood will begin to dry. With the drying comes shrinkage and the associated problems. Unfortunately, some changes in MC will occur no matter what. However, a change of + or – 2% in MC should not cause problems in the final product. When the MC changes more than that, problems are likely to begin to surface. The more the MC changes, the more noticeable the resulting problems will be. The bottom line is that air-dried lumber is likely to be not dry enough for most interior, home uses. Applying a finish to the product will not stop the moisture gains and losses but may slow it down somewhat. If the lumber is going to be used where the EMC is between 12 to 15% (such as an unheated shed) then air drying the lumber will be sufficient. Even if the lumber will have to be dried lower than what air drying will permit, the lumber can be air dried first to take advantage of free drying that Mother Nature provides.
There are a few points to keep in mind when air drying lumber to allow for maximum drying quality. Keep the lumber well supported in the packs with stickers about ¾" thick between each course of lumber. The stickers will allow air to flow between the courses of lumber to allow drying. Make sure to keep the stickers no more than two feet apart from each other. Having stickers every one foot is better and will provide more support. Keep the stickers in each course perfectly aligned with the stickers in the course above it and below it to distribute the weight evenly through the pack. This will help minimize warp. Protect the top of the pack from rain and sun and put as much weight on top of the lumber as possible. The purpose of the weight is to help alleviate cupping in the boards, particularly in the top few courses.
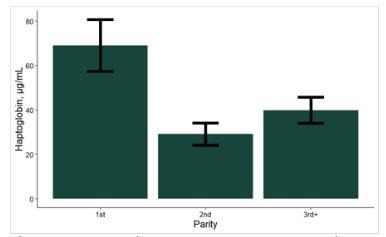
If whitewoods such as maple are to be air dried, try to start the air drying in the winter or spring when there is usually lower relative humidity and more air flow. Whitewoods are prone to fungal stain in the warm, humid conditions that are found in the summer. This will cause discoloration in the wood that will show up in the final product. If species that are prone to surface checking, such as oak, are being dried, the lumber may need to be placed in an area where it gets some air flow but not an excessive amount to help minimized the surface checks that will be developed. Using a wax end coating on the ends of the lumber can minimize end splits as the lumber dries as well.
The length of time it takes to air dry the lumber depends on the weather conditions, the species and thickness of the wood, and the location of the lumber while it is drying. It is often said that it takes one year for every inch in thickness. Most lumber will air dry much quicker than that. Poplar will dry faster than maple which dries faster than white oak. Monitoring the moisture content of the lumber is the only way to really know when the lumber is as dry as it is going to get through the air drying process. A future article will focus on monitoring the MC of lumber.
Source : psu.edu