The first operational efficiency measure that we compute is the gallons of ethanol produced per bushel of feedstock processed at dry mill plants. As noted above, monthly fuel ethanol production from the EIA does not distinguish between dry and wet mill ethanol plants. Consequently, we compute the ethanol conversion rate by dividing monthly ethanol production from the EIA by the bushels of corn and sorghum feedstock used at U.S. dry and wet mill ethanol plants from the USDA’s Grain Crushings and Co-Products Production report. Even though this computation is based on data from dry and wet mill ethanol plants, it should be an accurate reflection of the conversion rate for dry mill plants because, as shown earlier, wet mill plants represent less than 10 percent of total ethanol production. Note also that both corn and sorghum feedstock are included in the denominator because fuel ethanol production estimates from the EIA do not distinguish between feedstock used to make the ethanol. The amount of sorghum is usually quite small, typically no more than five million bushels per month, and no sorghum use has been reported since July 2020. By comparison, the amount of corn used in ethanol production generally is in the range of 400 to 500 million bushels per month. Finally, the EIA fuel ethanol production includes denaturant.
Figure 1 shows the estimated aggregate monthly conversion rate for ethanol per bushel of corn and sorghum feedstock at dry mill plants from October 2014 through December 2024, the latest month for which data is available. There is a clear upward trend over time, with the ethanol conversion rate steadily increasing from around 2.80 in late 2014 to a peak near 3.00 in mid-2019. This represents a about a 9 percent total increase in efficiency, or a gain of roughly 1.8 percent per year. There was a notable dip in the conversion rate during the initial stages of the coronavirus pandemic, but then the rate recovered steadily to a high of 2.99 in November 2024.
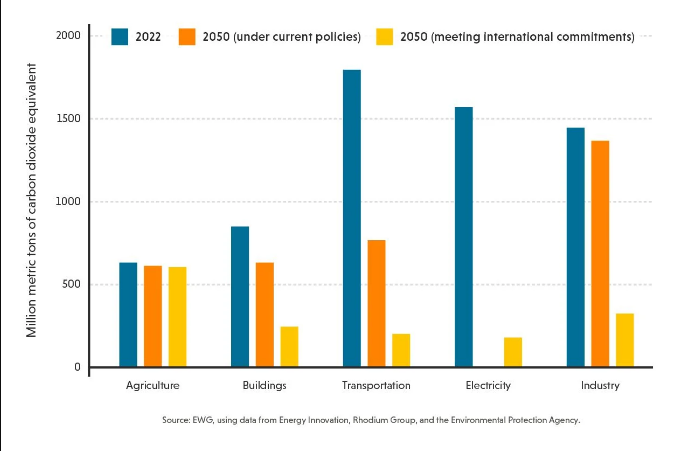
The second operational efficiency measure is the pounds of DDGS produced per bushel of corn and sorghum processed at dry mill plants. Computing the pounds of DDGS produced is complicated by the different types of distillers grains that are produced by dry mill ethanol plants. The Grain Crushings and Co-Products Production report lists five categories of distillers grain co-products for dry mill plants, so assumptions are needed in order to aggregate the different categories on a dry matter equivalent basis. It is assumed that condensed distillers solubles and distillers dried grains are components of DDGS, so we simply sum these two categories without adjustment and add them to DDGS production. We then adjust distillers wet grains with 65 percent or more moisture and modified distillers wet grains with 40 to 65 percent moisture to an equivalent dry matter for DDGS. Since DDGS has 10 percent moisture as a standard, we multiply the quantity of distillers wet grains with 65 percent or more moisture by 0.45 =1–(0.65-0.10) and modified distillers wet grains with 40 to 65 percent moister by 0.70 = 1–(0.40-0.10). We use conservative assumptions for moisture content to avoid under-estimating DDGS production on a dry matter equivalent basis.
Figure 2 shows the resulting aggregate monthly conversion rate for DDGS per bushel of corn and sorghum feedstock from dry mill ethanol plants over October 2014 through December 2024. Just the opposite of ethanol conversion rates, there is a clear downward trend in DDGS conversion rates. After appearing to bottom out in 2021 and early 2022, the rate continued its downward march through the end of 2024. The DDGS rate started at 17.34 pounds per bushel of corn in October 2014 and then declined to a low of 14.78 pounds in June 2024. This represents a 2.56 pound drop in DDGS production per bushel of corn, or a 15 percent decline. Finally, the linear trend regression shown in Figure 2 explains slightly more than 75 percent of the variation in the DDGS conversion rate over time.
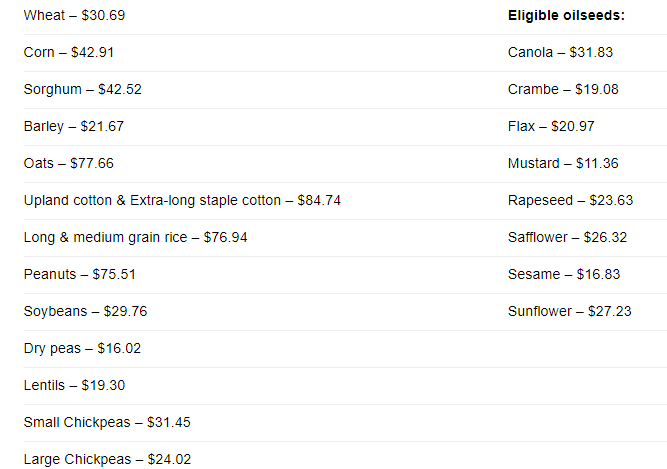
The third measure of operational efficiency is the pounds of corn oil produced per bushel of corn processed at dry mill ethanol plants. This is straightforward to compute as both components are reported directly in the Grain Crushings and Co-Products Production report. Figure 3 shows that the corn oil measure of operational efficiency had a non-linear trend over the sample period, with a period of very rapid growth from late 2014 through early 2018 and more modest growth thereafter. From the trough in December 2014 to the peak in December 2024, the corn oil conversion rate increased from 0.48 to 0.94 pounds per bushel of corn processed, or an increase of slightly more than 100 percent.
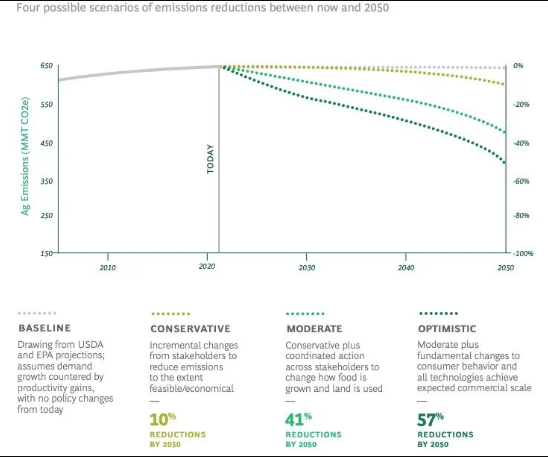
The fourth measure of operational efficiency is the pounds of CO2 produced per bushel of corn and sorghum processed at dry mill ethanol plants. Total CO2 production is aggregated across dry and wet mill ethanol plants in the Grain Crushings and Co-Products Production report, so it is not possible to compute CO2 production separately for dry mill ethanol plants. Using the combined total to represent CO2 production at dry mill plants is, once again, not expected to be a significant limitation because wet mill plants represent less than 10 percent of total ethanol production. Also, note that a technically more accurate description of the computed measure is the number of pounds of CO2 sold, since the amount of CO2 produced in ethanol production dwarfs what is sold into the industrial marketplace (farmdoc daily, March 15, 2023; February 19, 2024). As shown in Figure 4, the computed CO2 measure of operational efficiency is characterized by high volatility, with a peak of 1.32 pounds and a low of 0.80 pounds. There is a small upward trend over time, which mainly reflects a jump in the conversion rate that occurred in mid-2018. Nonetheless, the trend in the CO2 conversion rate over time is small compared to the other rates examine here.
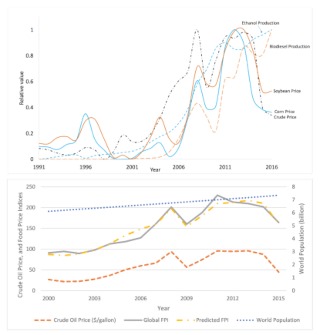
The picture that emerges from this analysis is one of tradeoffs in operational efficiency. These tradeoffs are most easily seen in Table 1, which presents annual averages for the four measures of operational efficiency for ethanol production at dry mill plants. Note that 2014 is omitted because a full year of data is not available from the USDA. Ethanol producers have clearly increased ethanol and corn oil conversion rates at the expense of DDGS conversion rates. Over the last 10 years, producers were able to net an additional 0.11 gallons of ethanol and 0.30 pounds of corn oil for each bushel of corn processed. This came at a cost of 1.81 pounds less DDGS.
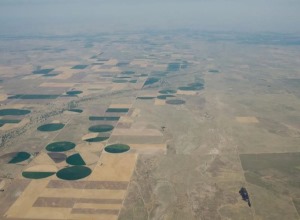
Presumably, the operational efficiency changes summarized in Table 1 were a rational response to the available technology for increasing production efficiency and the economic incentives for production of ethanol and corn oil versus DDGS. We provide a direct measure the economic impact of the operational efficiency tradeoffs with the aid of the revenues shown in Table 2. Revenues in Panel A are based on the product of annual average prices and observed conversion rates (Table 1) for each year. Note that we were unable to locate a price series for industrial CO2, and therefore, omit CO2 from the analysis. Given the small amounts of CO2 sold into the marketplace this is not a major limitation. The row listed for “Total” in Panel A shows the sum of the estimated revenues for ethanol, DDGS, and corn oil. Total revenue is estimated to have increased from $5.47 per bushel processed in 2015 to $6.26 in 2024, a net gain of $0.79.
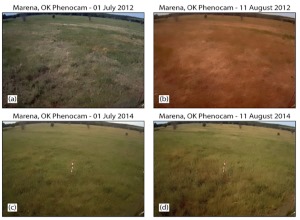
The revenue estimates in Panel B of Table 2 serve as controls for the analysis of the impact on revenue of the changes in operational efficiency. Specifically, revenues in Panel B are based on the product of annual average prices for each year and 2015 conversion rates (Table 1). In essence, this freezes the operational efficiency of the representative plant at 2015 levels. Total revenue under this alternative assumption is estimated to have increased from $5.47 per bushel processed in 2015 to $6.07 in 2024, a net gain of $0.60.
The key results of the analysis are found Panel C of Table 2, which shows the difference between the revenue streams based on observed conversion rates (Panel A) and the revenue streams based on 2015 conversion rates (Panel B). The difference identifies the gains/losses in revenue due to the changes in operational efficiency over time because prices are the same for both sets of revenue streams. The differences in Panel C show that the operational efficiency gains over the past decade led to an additional $0.18 of ethanol revenue and $0.15 of corn oil revenue per bushel of corn processed, or a total gain of $0.33. This was offset by a drop in DDGS revenue of -$0.14 per bushel processed. The net over 2015 through 2024 was a gain of $0.19 of revenue per bushel of corn that can be attributed to the changes in operational efficiency. This represents about a three percent improvement in total revenue, which is economically meaningful.
Implications
Recent trends in the operational efficiency of the U.S. ethanol industry are analyzed in this article. There is a clear upward trend over time in ethanol conversion rates at dry mill plants, which steadily increased from around 2.80 gallons per bushel of corn and sorghum in late 2014 to a peak near 3.00 in mid-2019 and again at the end of 2024. There was a notable dip in the conversion rate during the initial stages of the coronavirus pandemic, but the rate recovered steadily afterwards. Just the opposite of ethanol conversion rates, there is a clear downward trend in dried distillers grains with solubles (DDGS) conversion rates over time. The DDGS rate starts around 17.25 pounds per bushel of corn in 2014 and then declines to a low of 14.78 pounds in June 2024. This represents a 2.56 pound drop in DDGS production per bushel of corn, or a 15 percent decline. The most rapid gain in operational efficiency is associated with the corn oil conversion rate. From a low in December 2014 to the peak in December 2024, the corn oil conversion rate increased from 0.48 to 0.94 pounds per bushel of corn processed, or an increase of about 100 percent. The picture that emerges from the analysis is one of tradeoffs in operational efficiency of dry mill ethanol plants, with more ethanol and corn oil production coming at the expense of less DDGS. This is estimated to have netted ethanol producers an additional $0.19 of revenue per bushel of corn processed over the last decade.
Source : illinois.edu