By Jeff Lehmkuhler
Last month Dr. Bullock and I attended an evening program. One of the sponsors was a local feed company in which the owner had just taken over the company in January. Many of our communities have one of these local feed mills or dealerships. My brother and I both were fortunate to have had the opportunity from the Lubbers family to work in one of these feed mills while in school. This is one of the factors that sparked my interest in animal nutrition and helped set a path for my future career.
My rambling here is because of the recent Beef Bash information I shared, recent farmer meetings, and a string of emails regarding feed prices. My previous feed mill experience also plays a role having seen so many feed tickets. Two weeks ago, I asked a group of producers what they were paying for feed. They said that a bag of corn was $7-$8. Talking about prices on a “bag” unit or 50 pounds is normal for many of our beef operations buying feed for weaned calves or supplementing cows. There are 40 bags weighing 50 pounds in a ton. When you have unloaded as many semis of bagged feed as my brother and I did, you quickly memorized this as you had to count each stack of 10 bags as you wheeled 500 pounds down the ramp matching sure your unloaded inventory matched the billed amount.
The challenge of talking in bag units is that it can be difficult to relate to the feed prices in market reports. For instance, the Kentucky Ag Market Report lists prices for corn based on what elevators are buying corn for and not the price feed mills are selling corn to farmers. I would be asked to call the local Co-Op and find out what they were paying for corn, so Mr. Lubbers knew what to pay for corn hauled in to the mill to be competitive and how much to mark up the corn sold as feed.
If a local feed mill was buying corn locally for $5.60 per bushel and selling it for $7.00 per 50-pound bag, the price per ton would be $200 for the purchase price and $280 per ton back out the mill. This price difference is a 40% markup to cover shrink, storage, bagging, insurance, labor, and other business-related costs. However, when you just look at $5.60/bu versus $7/bag perhaps you think a little over a dollar difference is not a big deal.
We made a lot of different custom mixes for farmers. This intrigued me when I worked at the mill. One farmer would come down the steep hill with his old Johnny Popper pulling a cart of spelt. How many of you can say you have seen spelt? Others would back up with a truck load of ear corn for us to grind, some mixes we would have to grind hay into while others would be a simple mix of corn and a protein pellet.
Sorry for the tangent, I suppose age is catching up to me as I share too much of my past. Let’s talk about these local feed mill receipts. Many of you probably know how to read these, but others may not. The table below is a representation of a “ticket” or receipt used by many of the local feed dealers. The ticket includes how much, what was purchased/mixed, the price per unit and total amount.
Looking at the table, what feedstuff has the highest price listed? Soybean is listed at $30 and would be the highest price listed. This sparks the first common question, can I cut out the bean meal? The simple answer is yes. You can’t simply replace the soybean meal with a 1:1 swap with more distillers grain as soybean meal has about twice as much protein. To maintain the same protein level in the mix, we must add roughly 50 pounds of distillers grain and decrease another feed such as corn by 25 pounds along with removing the soybean meal.
The second highest priced feed is the mineral at $24. Since this is the only source of minerals and vitamin supplementation, there is not another feed listed that can be used as a substitute. Plus, when looking at the “Amount” column, the mineral is only $4.80 which is less than the soybean meal at $7.50. This should raise a red flag. How come there is more than twice as much soybean meal and the “Price” listed is higher by $6 but the amount is not more than twice as expensive?
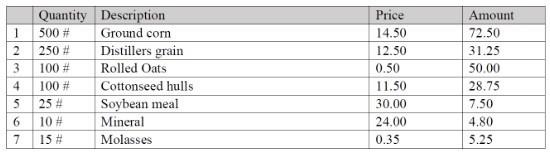
This is where not knowing the “unit” used to price the feed gets one in trouble. So, how do we determine the unit? Unit can be found by dividing the value in the “Amount” column by the value from the “Quantity” column. Next, divide the value in the “Price” column by your previous answer to get the unit. For soybean meal, the unit is found by dividing $7.50 by 25 pounds which is $0.30 per pound. By dividing the price per unit of $30 by $0.30/lb, the dollars cancel leaving 100 pounds as the unit used in the “Price” column. Let’s do the same thing for the mineral. The “Amount” column for mineral is $4.80 divided by the “Quantity” of 10 lb which is $0.48 per pound. Whoa wait a second, the mineral cost is more per pound than the soybean meal! Let’s finish to find the unit by dividing the price of $24 by $0.48/lb to get 50 pounds as the unit used in the “Price” column. Point – The mineral actually costs more than the soybean meal when pricing based on a common unit, price per pound or if you want to multiply by 2000 to get price per ton.
I want to continue to drive home the importance of understanding how to read these tickets. Let’s determine the unit and price per ton for both the cottonseed hulls with a listed price of $11.50 and dried distillers grains listed at $12.50. Again, quickly looking at just the “Price” column, one may be pondering if less distiller grains and more cottonseed hulls could be used. For cottonseed hulls, the amount is $28.75 divided by the quantity of 100 lb equals $0.2875 per pound. Dividing the price $11.50 by $0.2875/lb equals 40 pounds which seems like an odd number. Due to the low density and bulkiness, cottonseed hulls are marketed in 40-pound bags. To get the price per ton, multiply $0.2875/lb by 2,000 lb/ton which cancels out the pound units leaving $575 per ton. In late August, we bought a bag of
cottonseed hulls for the students to use in a starter diet for beef class and the price was equivalent to $480/ton. This is the cost of feedstuff with a nutritional value about the same as wheat straw.
To finish our comparison with the dried distillers grains, the amount listed of $31.25 is divided by 250 pounds from the “Quantity” column which is $0.125 per pound. The unit used in the price column is 100 pounds found by dividing the listed price $12.50 by $0.1250/lb. We already know that the cost per pound is drastically less than the cottonseed hulls and the price per ton is then $250. So, pondering how to increase the cottonseed hulls and lowering distillers grains was taking us down the wrong trail.
To wrap up, the other aspect is comparing feeds on a cost per unit of nutrient. To do this we will compare the two protein feeds in the table, soybean meal and distillers grains. Table values list soybean meal at 50-52% crude protein on a dry matter basis and dried distillers grains at 28-30%. If we assume 10% moisture in these feeds, the crude protein content as-fed would be 52*0.9 = 47% and 28*0.8 = 25%. On an as-fed basis, 2000 pounds per ton multiped by the crude protein percentage (47/100 and 25/100) will tell one the pounds of protein per ton. In this example, there would be 940 and 500 pounds of crude protein per ton, respectively for soybean meal and distillers grain. Dividing the cost per ton by the pounds of protein per ton equals the cost per pound of protein. Above we found the prices were $600 and $250 per ton for soybean meal and distillers grains, respectively. The cost per pound of protein is calculated to be $0.64 for soybean meal and $0.50 for distillers grains.
After taking the time reading this lengthy article, I hope that you have a better understanding of how to read those feed tickets. You may want to punch yourself for or the feed ticket for maybe having a more expensive feed that may be needed. However, understanding the cost of feeds and working with your nutritionist should provide you an opportunity to evaluate your feeding programs and develop feeding cost effective feed mixes to meet the needs of your livestock. Chat with your local feed dealer, county agent or nutritionist to evaluate options for your feeding program.
Source : osu.edu